How Can Automated Guided Vehicles (AGV) Be Effectively Introduced into Production Environments? - Part 2
12. 10. 2023
In our first tip on how AGVs can be effectively introduced into production environments, we highlighted the importance of analysing the current situation and suggested answering key questions regarding what we do and how we can facilitate the production process, as well as how internal logistics supports efficient production. In the present article, we highlight five elements or areas that require reflection prior to AGVs being introduced.
Automation Challenges and Key Considerations Prior to AGV Implementation
1. Familiarising ourselves with the key concepts
What does an autonomous transport system comprise?
- A multitude of autonomous mobile robots;
- Their periphery (charging stations, maintenance stations, etc.);
- Points or devices for interaction with the surroundings (permanent or temporary storage system/units, battery swap stations);
- A control system (Fleet Management System – FMS), which is responsible for optimising the overall logistical efficiency.
In rough terms, an automated guided vehicle (AGV) consists of a base unit and a manipulation unit. The base unit ensures movements in space, and the manipulation unit ensures a controlled contact with the cargo (handling), including pick-up and/or hand-over processes.
2. Identifying the KPI drivers that lead to thinking about introducing logistics automation
Let’s focus on what motivates us to introduce logistics automation or what we want to achieve with it.
- Is it the financial impact of reducing costs?
- Or do we want to ensure more controlled, accurate content (fewer errors), and just-in-time delivery (KANBAN)?
- Is the market dynamic intensifying? Are product exchanges becoming more frequent in production, thus requiring us to increase flexibility/responsiveness/reduction of adaptation time? Do we need a temporary warehouse to accommodate the demand of current peaks?
- Are the key issues the quantity and type of work that can be done in difficult conditions (night shifts, the complexity of the transhipment, a dangerous or unfriendly working environment marked by extreme temperatures or vapours)?
3. What is the object of logistics transhipment?
Let’s consider the following questions:
- Is there a single type of transhipment unit (unit of transhipment) or are there several different types? Is there a common denominator in terms of contact surfaces, identification markings (barcodes/inscriptions/QR codes, RF tags, etc.)? Is the unit of transhipment a dedicated piece, or a standard piece that is available on the market (e.g., a container/crate)?
- Is it necessary to consider future expansions? If so, what kind (weight/size/shape/materials)?
Example: a plastic crate (600x400x300mm) will be replaced by a cardboard box. - What are the quality and the time stability of the contact surfaces? Does the transport unit go through processes where it can get dirty/dusty/change colour? Is the material in the transhipment unit sensitive to vibration, impact or orientation?
- What is the stability of the material in the transhipment unit? Can we expect the material in the container to shift during the journey, thus exerting additional force on the vehicle?
Example: a small number of rather heavy metal pieces (e.g., screws) in a plastic container may slip and change their position in the event of excessive deceleration. When they impact the sides of the transport unit they generate large impact forces that the contact surfaces must withstand, so as not to result in uncontrolled loss or instability of the load on the vehicle. - Is it possible to expect material in positions outside the transport unit’s loading gauge (e.g., in the transhipment of items packed in vacuum bags, where they are pressed inside when they are loaded and may later on peek out of the box)? Is the transhipment unit part of an internal process flow in which we can ensure a controlled condition and quantity, or is it part of an open customer/subcontractor swap system where the state of play has yet to be identified (possible damage, visibility of markings, satisfactory condition of contact surfaces)?
4. Our logistics operation environment is …
- A new production environment
Consider the specific preconditions that a particular technology requires for efficient use (spatial conditions, climate, security, energy, etc.). These are fairly easy to ensure in the case of construction of new facilities. In real life, however, these preconditions are rarely met, as the investment costs of a facility often exceed the investment in technology, thus reducing the investment’s ROI and consequently decreasing its ‘attractiveness’.
- An existing production environment
A much more realistic scenario is that the introduction of new technologies takes place in existing production environments. There are two main reasons for this: the first is the limited scope of the investment, and the second is the dedicated testing of the technology and its placement on a small scale to resolve teething problems and thus control the risks associated with it and keep them at a manageable level.
With an existing production environment, we need to keep the following considerations in mind:
- Does the old system allow for the introduction of automated transport?
- Is it possible, at least in part, to provide spatial-temporal sharing with existing processes? In terms of safety, as well as priority and avoidance rules, to what extent will the existing processes also need to be adapted? How much effort will the re-education of employees require?
- How will we establish the cooperation of humans and machines so that their coexistence and harmony is possible and above all – desirable?
- In mixed systems, who bears the responsibility for the effectiveness of the newly introduced system and for the impact on the system already in place? What are the influence factors, and can we have a conscious impact on them?
- The potential impacts on changes in the assessment of the risks to safety and health at work should be examined, and the safety of equipment and adequate fire safety should be ensured.
5. Assess the level of process flexibility
In assessing the level of process flexibility, consideration should be given to the dynamics of the target logistics process (storage/transhipment/delivery):
- Is the process steady or does it vary?
- Are the timing and magnitude of the variations known?
- To what extent do the rhythms of product batch exchange affect the logistics process?
- Can these variations (in product types, transport units) be covered with the same transport devices?
- To what extent do the input/output locations, as well as the necessary ‘buffers’, change?
- Is the pick-up/loading system similar?
- Do we have a sufficient number of fixed navigation support points? Have we ensured that they are not obstructed by deposits of material?
- Is there a human being in the logistics operation environment?
- If we have chosen a limited range of processes and environments for the first pilot project, do we want to prepare the system for future expansion?
- Will it be merely expansion, or – if it proves necessary – will it involve a dynamic exchange of resources?
There are many challenges involved in logistics automation. Our next article will present five of the key challenges.
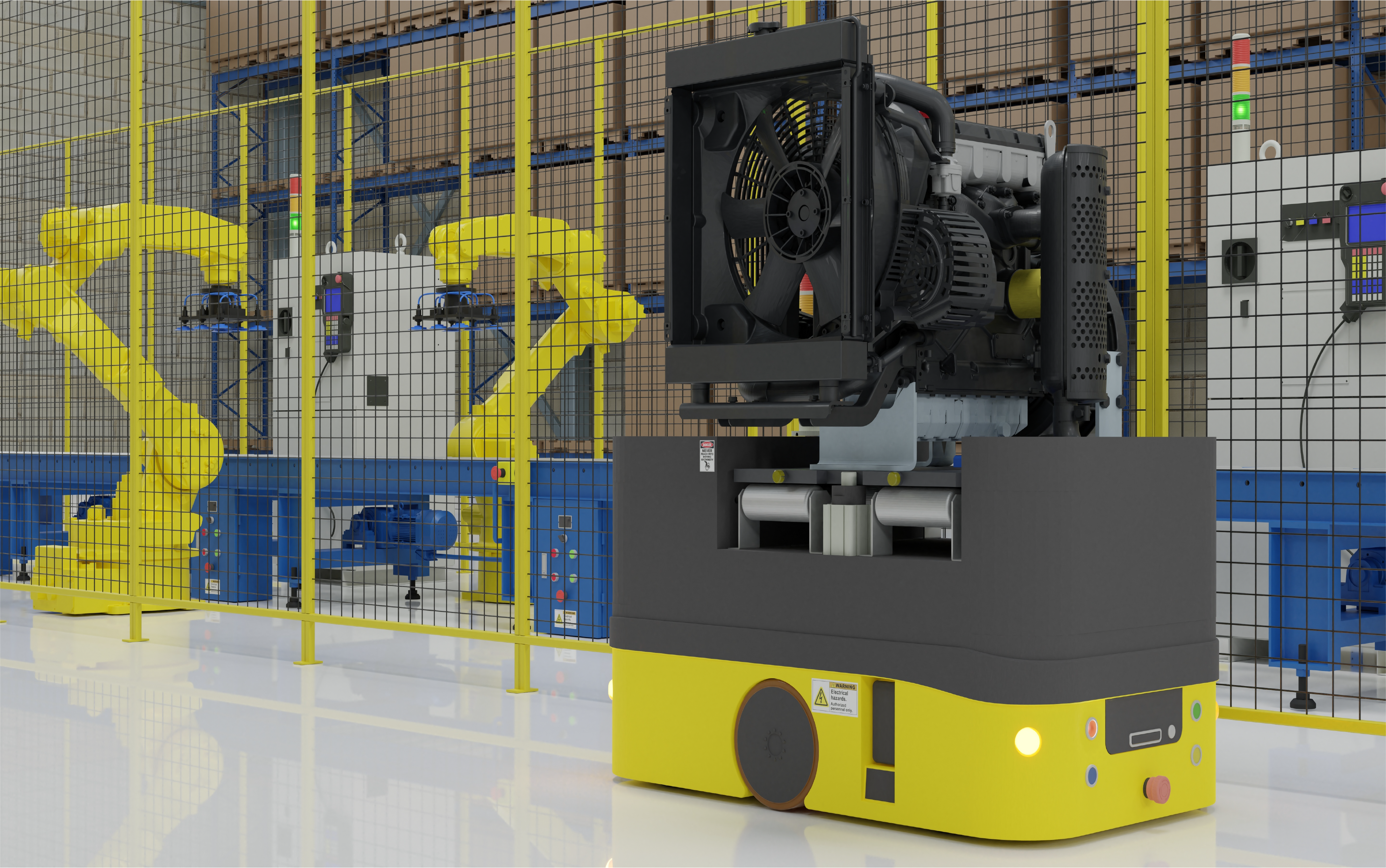