How Can Automated Guided Vehicles (AGV) Be Effectively Introduced into Production Environments? - Part 3
09. 05. 2024
Let’s remind ourselves of the five elements or areas that require reflection prior to AGVs being introduced, as outlined in our previous article on the topic of how Automated Guided Vehicles (AGVs) can be effectively introduced into production environments:
1. Familiarising ourselves with the key concepts. 2. Identifying the KPI drivers that lead to thinking about introducing logistics automation. 3. What is the object of logistics transhipment? 4. What is our logistics operation environment like? 5. Assessing the level of process flexibility.
This time, let's learn about five key challenges of logistics automation.
Five Key Challenges in Logistics Automation
- Market dynamics
Overall, the dynamics of needs in production processes are increasing. This is characterised by the pace of trend change and faster (i.e., shorter) product life cycles, online sales and e-commerce, high levels of individualisation of products, etc. These changing needs bring many new challenges to manufacturing logistics.
- Level of computerisation of the production environment
If we want to make the most of logistics automation, we need to ensure adequate coverage of all boundaries of the system with appropriate information support.
That is why we need automatic optimisation and assignment of transport orders from the top. In the operational part, we need interaction between humans and the devices that control the interaction between the material (on-demand procurement/delivery through KANBAN, just in time delivery, safe transfer) and its surroundings in terms of sensing safety risk areas, alerting to the presence of unforeseen obstacles, and dynamic avoidance of such obstacles.
- Interaction with human beings, planning and sensing the environment in real time
Automatic identification of the actual situation in the surroundings is crucial in dynamic and mixed environments with human beings. Firstly, because it is difficult to make a correct inventory of everything. Secondly, because everything is changing, so the rules can quickly become obsolete. Thirdly, because part of the dynamic is caused by ad-hoc interactions and decisions.
In order for the system to function successfully, it is necessary to ensure that no action of the system occurs in an uncontrolled way, as this can lead to risky operations for the system in terms of security, and in the worst-case scenario to security risk operations for human beings.
Examples: Is the route in front of the vehicle free? This is most often checked at ankle level, but what about parts protruding from shelves? Can small, sharp objects be detected? Can fast-moving objects on the route also be detected?
Based on past dynamics, can we predict the surrounding environmental behaviour that determines the level of risk, so that we are not in the position of only giving stop-start commands (1/0), which often lead to system blocking?
Do we know what is going on with the object of transhipment? Can we trust the projected load weight and its planned distribution? What if overload occurs, or if it arises due to the dynamics of the vehicle?
Since environment sensing is always associated with a degree of uncertainty in the measurement process, it can be improved by parallel measurements of the same objects by different methods and/or sensing devices.
Example: unlike 2D-laser sensing, 2D-optical imaging with cameras is very sensitive to lighting conditions, enabling us to dynamically check the confidence level and adjust the interaction speed or mode accordingly. Confidence in the correctness of measurements can be further improved by correlating planned simulation forecasts, or by taking into account the physical nature of relationships between objects (where certain objects should be located).
- Implementation
In complex applications, such as automated guided driving with material and human interaction, we can conclude that there are no bad products (i.e., AGVs) on the market. The key difference between them is whether there is a team available with sufficient expertise and enough team members to implement the project of introducing AGVs into your production environment within the set deadlines and at the prescribed level of quality – on the precondition that most of the risks have already been identified and eliminated.
- Process control and optimisation
In addition to meeting the functional requirements of automated logistics transhipment, the system must also provide all necessary maintenance and optimisation subsystems. These include analytical tools for the multitude of components and their interaction, control of component status (identification, maintenance, registration), and the possibility to influence components (switching on/off, dedicated self-testing), as well as manual intervention in the optimisation process with the ability to force orders, track users and record events for the purpose of analysis and searching for causes in the event of failures or accidents.
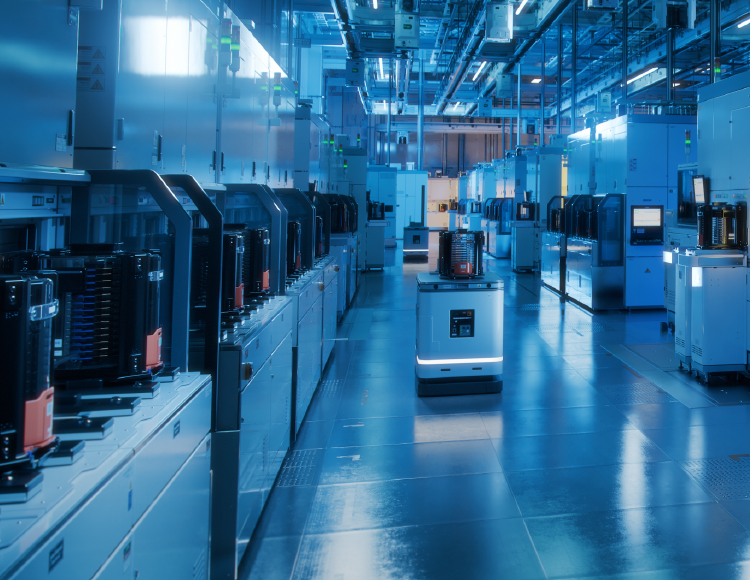