A Hi-Tech cheese production plant in Israel supported with our know-how
08. 10. 2018
Tnuva, the largest food corporation in Israel, has built a new high-technology plant for the production of cheese in Tel Yosef, with fully automated production, warehousing and dispatch.
Epilog contributed to establishing the plant. We implemented a central information system specifically tailored to the company’s needs, which coordinates the work in the logistics part of the plant, taking care of the warehousing, dispatch and internal logistics. A series of conveyor belts, lifts and automated guided vehicles (AGVs) take care of the transport of finished products, i.e., blocks and slices of cheese. The entire process is supported by high-performance information systems and software managing their operation, and our Atlas WMS package is responsible for the coordination and exchange of data.
Atlas WMS Ensures Smooth Running
Atlas WMS is responsible for all of the logistics in the warehouse: it allocates transport orders to AGV units in an optimal way, takes care of the automatic replacement of empty containers to where palettes are located, and manages the transport of palettes and packaging material according to process requirements. In addition, it makes sure that the automated high-rack warehouse of empty containers is used in an optimal way. At workstations around the plant, it enables users to interact with the system, to control and visualise automated devices, and to have an overview of the current and past stock.
Automated Guided Vehicles under Control
During the project, we developed a number of new technological solutions and upgrades. Tnuva is the first project in which we have controlled the operation of AGVs, giving us an opportunity to acquire valuable experience and knowledge about how automated guided vehicles function. We also successfully implemented links to numerous devices, lifts, robots, and transport lines that were new for us.
Additionally, we developed a new method of data exchange with Manufacturing Execution System (MES) where message structure is formally defined using standard definition language (XML) that allows us and our partner to independently test data and structure accuracy.
A new visualisation platform was created for an overview and visualisation of the situation in the warehouse. It works as an independent online application and enables the monitoring of the situation via an online browser. This application has also been adapted for mobile phones.
100 Suppliers from 10 Countries Participated in the Project
According to Tnuva, the new Tel Yosef plant, one of the most advanced in the world, represents a milestone in promoting the Israeli and international food industry. At the opening ceremony, Anat Gross-Shon, Manager of the Milk Business and Marketing Division, said: “The advanced technologies in the new plant will enable us to further diversify products and expand kosher certifications, and will serve as a platform for creating differentiation and product innovation, which will become evident in the coming year.”
The importance of this plant is further demonstrated by the impressive figures presented on the company’s website: they cut approximately a billion slices of yellow cheese a year and produce around seven million chunks of cheese a year. The technical side is no less interesting, as the project saw the participation of 100 suppliers and contractors from 10 different countries, together boasting some 230 years of cumulative engineering experience.
A Complex Project in the Food Industry Completed with Distinction
Despite the fact that, until now, we have not implemented many projects in the food industry, we enthusiastically and successfully tackled new processes and terminology in this line of work, as well as the specific features of kosher food. The project was also rather demanding in terms of the coordination of work, as we not only worked with Tnuva but also with companies such as IHS, Matrix, E&K, and others. Another challenge, which during the project turned into one of the most valuable experiences, was the different cultural environment.
Equipped with expertise on the operation of AGVs, the food industry and the Middle East, we are now ready for new achievements and challenges in the developing activities and in culturally different, yet interesting markets.
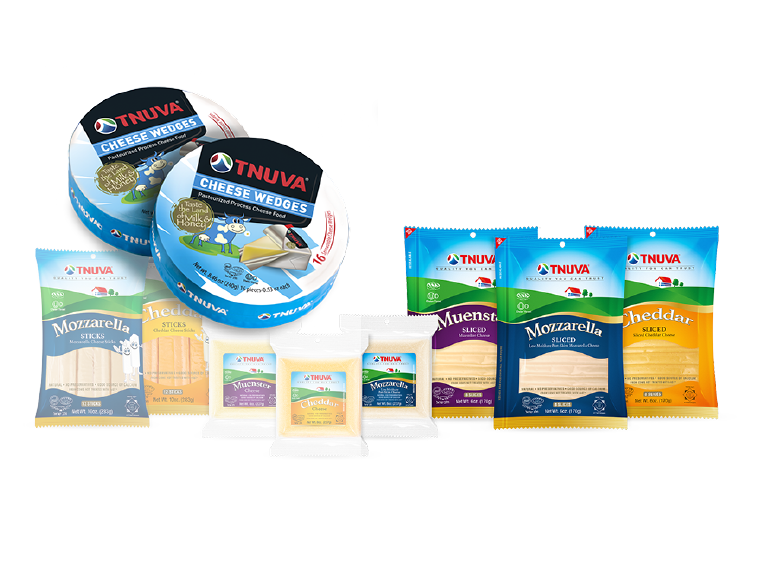