Successfully Implemented Warehouse Management System in Hydro Belgium
19. 01. 2021
Before the introduction of the new ERP system, Hydro Belgium, part of Norsk Hydro corporation, also decided to modernise their warehouse management system. They introduced the Atlas WMS solution to improve warehouse efficiency and picking, as well as to ensure 100% traceability of the material throughout all finishing processes (sawing, wet painting, thermal treatment, etc.) carried out in Landen. With the help of Epilog’s flexible development team and with the adaptability of the Atlas WMS solution, they were able to meet their various needs, including the requirement for an unchanged process of planning the supply of the production line for the powder coating, wet painting and preparation of profiles for the thermal bridge breaking process.
Norsk Hydro, which employs 35,000 people in total, is present in 140 locations in 40 countries around the world. It works in various market segments, such as aluminium, energy, metal recycling, renewable energy sources, batteries and others.
Hydro Belgium, with its locations in Belgium, offers a wide range of innovative, reliable and aesthetically sophisticated aluminium systems for walls, facades, windows and doors, which they supply to architects, the metal industry, investors and end customers worldwide. Their logistics and administrative centre is in the city of Landen. The site is a combination of a warehouse and a manufacturing plant where semi-finished products are processed into finished products and wet painted . We talked to our Project Manager, about what the introduction of Atlas WMS made easier for Hydro Belgium.
Why have Hydro Belgium decided to improve the efficiency of their warehouse, have an overview of the material flow at all times, and achieve better transport capacity utilisation?
Norsk Hydro’s strategy is to unify ERP systems at the level of all companies and switch to the SAP solution. Before making this step, Hydro Belgium also decided to make an additional big move: to replace the existing warehouse management system. They were using Dynamics AX (as ERP and WMS) for the manual part of the warehouse, and Egemin WMS for managing the automated warehouse. In addition to low efficiency, Dynamics required a lot of paperwork; and with Egemin they were faced with unreliability and a lack of support. As the picking process was not transparent, they had semi-full containers and palettes, which resulted in a low transport capacity utilisation rate.
Why is Atlas WMS the right solution for them?
They were looking for a solution that would effectively cover the manual and automated parts of the warehouse and ensure 100% traceability of the material flow through the finishing processes. They wanted the production supply planning procedures to be maintained for the wet painting and preparation of profiles for the so-called thermal bridge breaking process.
They chose our Atlas WMS warehouse management system for several reasons. They were convinced by our experience with SAP integration and automated warehouses, as well as with the integration of production processes and material flow control. We assured them that their challenges could be solved and their requirements met. Any remaining doubt was dispelled by our successful implementation projects at Wicona and Hydro UK. The ice was broken, our cooperation was underway.
Has the Atlas WMS warehouse management system met their specific requirements and ensured 100% traceability of the material through production processes as well?
We approached the customer’s requirements with several adaptations to their specific needs and enabled them to make as smooth and painless a transition to the new solution as possible. Easy searching and good data overview is provided by Atlas GUI (graphical user interface) and the Atlas RF terminals ensure quick and easy work.
What four key improvements have been made by the introduction of Atlas WMS?
- Warehouse transparency, simpler picking, packaging and loading procedures
Atlas WMS fully manages the container shipping area at the locations and controls residues and packages until they are loaded onto the truck. Picking and packaging is carried out by different people in different parts of the warehouse with a time delay. The increased utilisation of transport capacity (containers and palettes) was achieved by consolidating the material after picking and locking the material carrier only once it is full.
Once the picking is completed, e.g., for final customers, Atlas WMS enables the consolidation of the material before packaging. The user can see the extent to which each material carrier (cassette, palette) has been filled and where it is located. Thus, they can combine the material on carriers to increase transport capacity utilisation, i.e., use a smaller number of cassettes or palettes on a truck. In doing so, Atlas WMS complies with the rules for the pooling or packaging of material (same order, customer, or route).
Stock falling below the minimum quantity is supplemented from stock in the central warehouse and the palette warehouse. The user has an overview at all times of where stock is below the minimum quantity and can simply create orders to replenish stock. If stock drops below the minimum quantity during picking or moving, Atlas WMS automatically creates a stock replenishment order.
Atlas WMS also allows individual items to be fixed to specific locations by clearly indicating the relevant locations of each item when the item is put in its place or picked.
When creating picking orders, different warehouse areas, material types, final destinations and order types are taken into account. Depending on these parameters, separate pick sheets are created. - 100% traceability of the material through production processes
With Atlas WMS the client has fully supported finishing processes: profile sawing and finishing for thermal bridge breaking, kitting, and supply of material to the internal line for wet painting, as well as to external units for wet painting.
For each type of production, we supported different production supply rules with separate planning input masks. In doing so, we followed the rule that materials of different colours should not be mixed in the same carrier (stillage, mobile rack). For the thermal bridge breaking process, however, the picking orders combine the material needed in the production line, which reduces the number of picks.
We accommodated the client’s wish to retain the process of planning production line supply for wet painting and preparing profiles for the thermal bridge breaking process by developing a special interface for communication between Atlas WMS and the Wet-Painting Line Management (SuTso) application to simplify the user’s process of taking material from painting. Excel spreadsheets for planning further processing of painted material at the thermal break line have now been replaced with Atlas WMS. The customer has thus simplified the picking and dispatching of packages. - Automated distribution of material for clients and stock
After completion of the production process, Atlas WMS creates orders for the movement of the material to a specific area of the warehouse, depending on the product. If there is a customer order for a certain product, an order is created to move the product to the packaging area next to the material for the same customer. In the case of production for stock, where there are no orders for the product, an order is created for the movement to the warehouse (manually or automatically, depending on the material setting). This was not possible with the previous system. - Support for the existing CMR document printout
Despite the Covid-19 pandemic, the project was successfully implemented and put into operation. We found the right time for our implementation team to travel to Belgium, and they successfully completed the work and returned home healthy.
We remain in contact with the client even after implementation and support them in the integration of SAP with Atlas WMS. Once the transition to SAP has been completed, we plan to continue our cooperation, as we have proposed some further improvements to our client. Since the whole project would be too comprehensive if it coincided with the customer’s integration of the new ERP system, we have divided it into two stages. After successfully completing the first stage, we are now looking forward to the second.
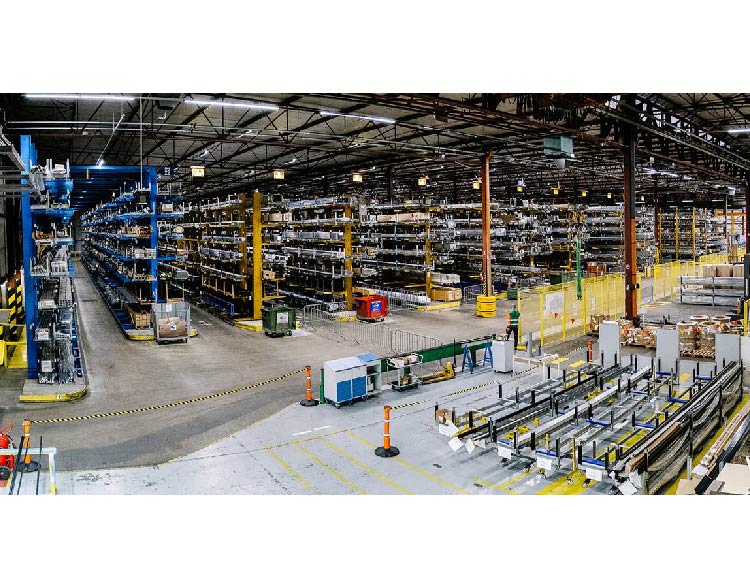