Supplying production through an information system for warehouse management
22. 04. 2024
To be competitive in the market, companies are constantly looking for ways to optimise their processes. Optimisation cannot be achieved without digital transformation, but this does not happen overnight. Danfoss Trata and Epilog are well aware of this. Together, with long-term committed cooperation and determination, they are progressing step by step on the path to a fully automated warehouse in Danfoss Trata.
We talked to Dr Domen Marinčič, Project Manager at Epilog, about what their cooperation and long-term partnership looks like in practice.
(The interview, in Slovenian, was published in the journal Logistika Magazin, March 2024.)
What were the first steps in automating the warehouse at Danfoss Trata? How did you approach the project?
In line with their strategy and digitalisation goals, Danfoss Trata wanted to automate their manual warehouse – their “supermarket”, as they call it – that supplies production. Already in 2019, we implemented a project for them to manage an automatic high-rack MINILOAD warehouse system for crates with materials for production – automation replaced their previous manual warehouse "supermarket".
What were the first results of that project?
By establishing an automated MINILOAD warehouse, they significantly improved the speed of work, the accuracy of process execution and the overview of the inventory. In addition, the capacity of the warehouse was increased.
What came next?
A year later, in 2020, we signed an agreement to upgrade Atlas WMS, our IT solution for managing and monitoring all logistics processes, so that the system would manage all of their internal logistics processes – from the receipt of raw materials, the placement in storage in manual and automated warehouses, picking processes and production logistics processes, to all of the processes running in the finished product warehouses and dispatch. The project went live at the end of June 2020.
We integrated Atlas WMS with Danfoss’s single global One ERP system (SAP HANA), making it one of the key pillars of the digitalised information infrastructure of Industry 4.0.
We also introduced automated material delivery to production lines using autonomous mobile robots (AMRs).
In addition, we carried out a project to optimise storage within the MINILOAD warehouse system in order to achieve faster delivery times. This means that automated reorganisation of the material is triggered in the MINILOAD system outside working hours. The material that will be first in line for the production line the next day is redistributed by the automated warehouse so that it is the first material at the picking locations the next day.
How did you approach the challenges in the final phase, the so-called go-live?
The biggest challenge in introducing Atlas WMS was to establish a smooth workflow, without downtime. Key to the successful integration was working closely with the Danfoss Trata team and gaining an in-depth understanding of their processes. The transition to the new system was carefully planned and prior extensive testing was carried out in a test environment before implementation. This allowed us to respond effectively to any unforeseen situations and ensure a smooth transition period without major setbacks. Already on the third day after the start-up, the work was carried out without any major problems that might affect its efficiency.
The key challenges of modern production are precisely in logistics, as 80% of all operations are of a logistic nature. How can the right material be delivered at the right time to the right place?
In Danfoss Trata, the classic solution for the supply of material in advance, i.e., "just in case" (push), was replaced by a modern concept of lean logistics called the pull system. We take care of the optimal stock level using the Kanban method. Every production cell on the production line uses triggers in Atlas WMS to report the need for raw material movements from warehouses to production. Once the material is picked for production, Atlas WMS creates an order to transport it to the production line.
The introduction of the pull system has improved the punctuality of deliveries (on-time) and the reliability of the entire supply chain in production.
In this case, a WMS is more than just a classic warehouse management system, as it can also supply production. What else have you developed or adapted for Danfoss Trata?
It is true that, in our case, the WMS is much more than just a warehouse management system, as it manages the entire internal logistics. In Danfoss, it also takes care of classic warehouse processes, especially for the supply of production.
Atlas WMS makes sure that the material is where it needs to be: on specific production lines at a specific time.
In addition, in Danfoss Trata, for example, automated wrapping and labelling of pallets of finished products for customers takes place via Atlas WMS. Based on an order from Atlas WMS, the pallet is delivered to a wrapping conveyor, where it is weighed and measured. The pallet is then conveyed to an automatic foil wrapper, where the SSCC code is first automatically scanned, after which the pallet is wrapped. Atlas WMS also arranges for the design of printed labels and the transfer of the necessary information to SAP, as well as for the removal of stock from the accounts.
You mentioned the introduction of AMRs. Does this also bring about larger storage and/or production areas?
This is what we all want, but the reality is usually different – limited production and storage space is one of the major obstacles for Danfoss Trata for objective reasons, but we are trying to solve it – to overcome it with optimisations in Atlas WMS. With innovative solutions and competent employees and partners, we can optimise intralogistic processes even in the existing space, which is often limited. With Danfoss Trata, we have been able to do just that.
How the warehouse automation process is perceived in Danfoss Trata is described by their Logistics Technology engineer Martin Štular. “Atlas WMS as a modern warehouse system is a step forward in the development of internal logistics, which began with the implementation of MINILOAD. The system represents the centre of all of the processes carried out in internal logistics, while also being a good basis for its further development. By connecting it with the production MES system, we have gained greater control over material flows in warehouses and production. From now on, we are no longer dependent on paper information in internal logistics, as the systems send data to each other automatically. In terms of the timeline, the project was very ambitious. A lot of our employees from different departments of Danfoss Trata were involved.”
Danfoss Trata is part of the Danish multinational Danfoss. The company develops and manufactures products for the regulation of heat transfer in district heating systems. All activities, including the supply chain, are carried out in accordance with their vision: to create the engineering of the future. They started their digital transformation as early as in 2016.
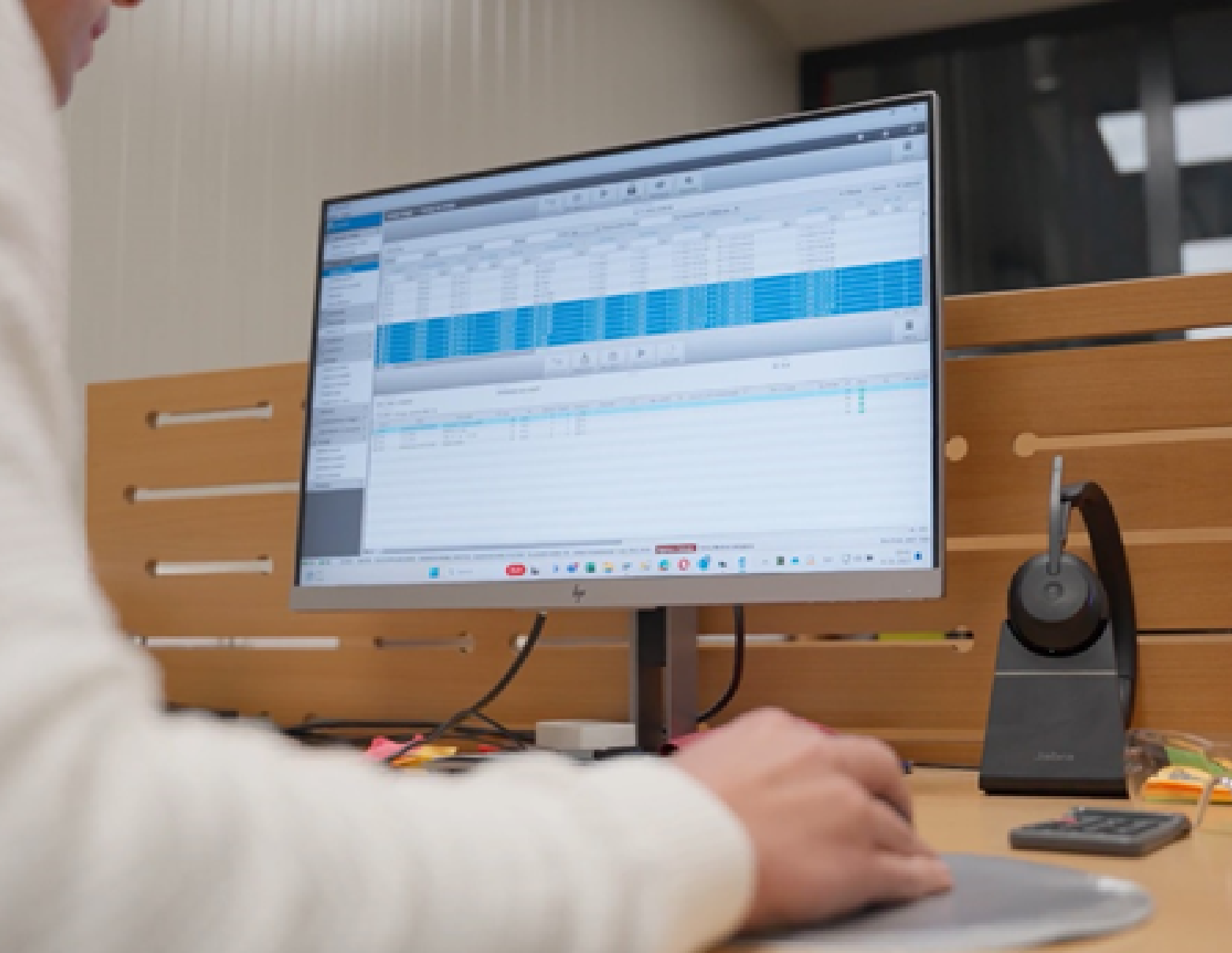