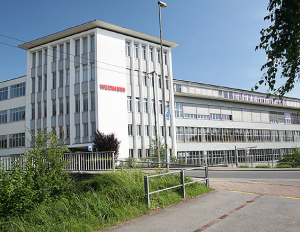
Weidmann: Strategic Upgrade of Atlas WMS for Long-Term Efficiency
Weidmann Electrical Technology AG, a leading global manufacturer of electrical insulation solutions, has consolidated its commitment to technological excellence by upgrading its Atlas WMS to Gen5, the latest generation. In cooperation with Epilog, the company has successfully implemented a system upgrade at their plant in Rapperswil, Switzerland. This ensures the continued reliability, improved user experience and long-term stability of the system – without any disruptions to production. More